As a promising alternative to Li-ion, the use of lithium metal negative electrode is expected to bring a major breakthrough in terms of performances and will be key while developing high energy density post-Li-ion systems such as high energy cathode materials, solid-state systems, lithium/sulfur (Li/S) and lithium/oxygen batteries. That said, issues of lithium metal reliability and cyclability have also been pointed out in the past, and ensuring a commercial reality means mastering the lithium anode.
The challenge of controlling the lithium metal anode has already been partly solved by BlueSolutions with their successful solid-state Lithium Metal Polymer (LMP®) technology. This commercial system is based on the use of an iron-based abundant, cheap and non-toxic positive electrode material (LiFePO4), a thin polymer electrolyte film and a lithium metal foil. LMP® cells are produced by extrusion, which is a clean solvent-free process with high production yields. In order to increase the energy density of LMP® batteries, additional breakthroughs are needed.
For this purpose, the ALIM project aims at supporting the production of advanced lithium metal negative electrodes and the commercialization of Critical Raw Materials (CRM)-free innovative battery solutions for both 'Mobility' and 'Energy' applications:
1- By reducing the lithium electrode thickness as compare to state-of-the art and already existing commercial products, while maintaining the production yield and quality level required at BlueSolutions.
2 -By evaluating a change in the cathode chemistry from LiFePO4 to sulfur, this will allow to boost the energy density of lithium metal batteries, while maintaining low cost, environmental friendliness and CRM substitution too.
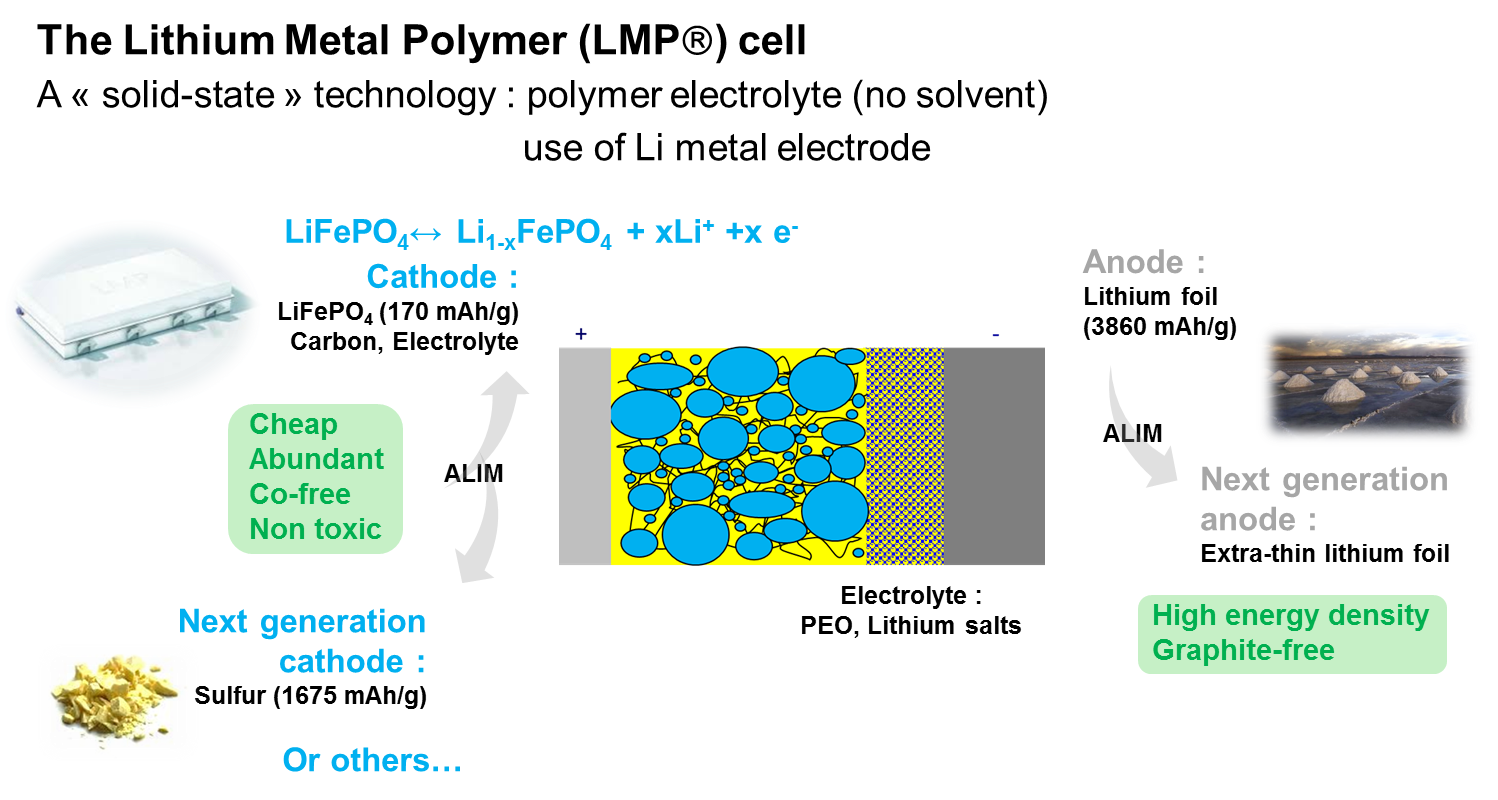